Storage Combustible & Flammable Liquids
Flammable liquids storage rooms are present in many of today’s industrial installations. Liquids that can be stored in small drums or in large storage tanks represent a risk of fire that should be carefully addressed by the designer.
Sprinkler systems represent a simple solution for many of these installations to control the fire, but what the designer often requires is to actually extinguish the fire quickly in order to minimize fire damages to the facility and downtime, not simply control the fire until the fire department shows up.
The following case study describes the use of the Compressed Air Foam (CAF) technology installed in an underground oil storage facility and highlights the advantages of this design compared to other available technologies.
Application
Fire protection was required in an existing underground facility used for bulk storage of transformer oil in ten (10) large tanks of 30,2 L capacity each.
Room dimensions were 25M long by 10M wide with a ceiling at 4,5M, constructed of concrete. Also, part of the hazard was an access tunnel measuring 8M long by 1,5M wide with a ceiling at 9 feet, constructed of concrete as well.
Problems
with the use traditional technologies
This hazard could theoretically have been protected with either of these two typical methods:
- Low Expansion Foam
A low expansion AFFF foam-water sprinkler system designed as per NFPA-11 with a density of 0.16 gpm / square feet, discharging during 60 minutes (AFFF stands for Aqueous Film Forming Foam and is a fire fighting foam widely used to extinguish fires in hydrocarbon fuels).
The main problem with this design was the high cost of the infrastructure that would be required to collect and drain the foam-water solution. Indeed, the drainage system was never designed to handle the high volume of water produced by the discharge of a typical foam-water sprinkler system and the cost of upgrading its drainage system would have been prohibitive, which is a common issue in existing facilities. - High Expansion Foam
A high expansion foam system designed as per NFPA-11 to completely flood the area, discharging during 12 minutes.
While partially resolving the issue of water drainage with a water flow of 250 gpm, the main problem with this type of system was the difficulty of physically installing the large volume air receivers necessary for such a system.
Also, an issue was the reluctance of the local fire marshal to send a fire fighter squad in an underground facility filled to the ceiling with foam, to fight a fire they cannot see. Compounding the problem was the real possibility of spatial disorientation for the squad in such an environment during a fire.
High expansion foam systems indeed do represent a problem in confined and cluttered spaces such as these.
Designing
With ICAF
A solution to these problems exists by using FireFlex Systems ICAF Integrated Compressed Air Foam system for fixed piping networks.
This new FM Approved AFFF foam system can be designed to protect this area using NFPA-11 TIA #05- 1, and FireFlex Systems ICAF Design Manual. Article 7.16 of the TIA states that the system shall be designed to discharge compressed air foam for a minimum period of 10 minutes for this type of application.
Based on a nominal flow of 22,7 L/min per nozzle, the total water flow required for this application was limited to 726,8 L/min. Using TAR-225C Nozzles, the whole storage area is covered using 32 nozzles as shown in Figure 1 (see below).
This is a consideration that the designer always has to keep in mind as it is an important part of what is considered good design and engineering practices. A subsequent discharge test proved that the design covered every area adequately with compressed air foam.
An additional four nozzles were used to cover the access tunnel leading to the protected room.
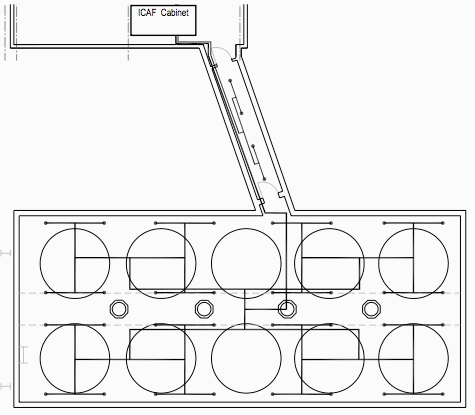
Figure 1
Detail of the CAF Nozzles balanced layout
Conclusions
The selection of the ICAF System represented the ideal solution for the protection of such a facility which otherwise would not have been protected at all, or at much greater cost for the owner.
Not only was the installation substantially less cost, but it also prevented major infrastructure modifications to the existing facility. Such considerations are often neglected by the designer in the feasibility studies for the installation of fire protection systems in special hazards.
Considerations would also have to have been made for the water supply portion of the installation.
Indeed, the supply and installation of fire pumps (vertical turbine or diesel powered), water storage tanks and redundancy would have increased the costs dramatically ! Those were not required by using an ICAF System to protect the facility.
Containment, collection and drainage of all that water is also an issue that is often neglected. The existing drainage system in this application was able to handle the small additional amount of water used by the ICAF System, but not from a typical Foam-Water System.
Should the High Expansion Foam System been retained as a solution, air intakes and exhaust louvers would have been required and the installation of these was more than problematic in this environment. The issue of visibility for safe evacuation of the occupants was also present.
Installation of the ICAF System proved to be easy for the contractor, using standard sprinkler piping and hangers and in the end, offering better fire protection without the associated water damage. ICAF Systems only need a small quantity of foam concentrate to be kept in storage which is another advantage.
The physical layout of the facility also mandated to install the system hardware (foam tank, system trim, etc.) almost 200 feet (60m) from the hazard itself. With the use of the ICAF System, this was not a problem at all since long pipe lengths between the system and the protected hazard are easily handled and do not represent a design problem due to excessive pressure losses as in foam-water systems.
Piping was kept to minimal diameter with no detrimental effect on the system performance. Should you have questions regarding this application or any other involving flammable liquid hazards, contact SIRON Compressed Air Foam. Our engineers will work the project out with you and find the best layout for your specific application.